The appearance design of lenses plays a crucial role in modern optical devices, with plastic and metal being two predominant material choices. The distinctions between these two types are evident across various dimensions, including material properties, durability, weight, cost, and thermal performance. This paper will provide an in-depth analysis of these differences while evaluating the advantages and disadvantages of each type in conjunction with practical application scenarios.
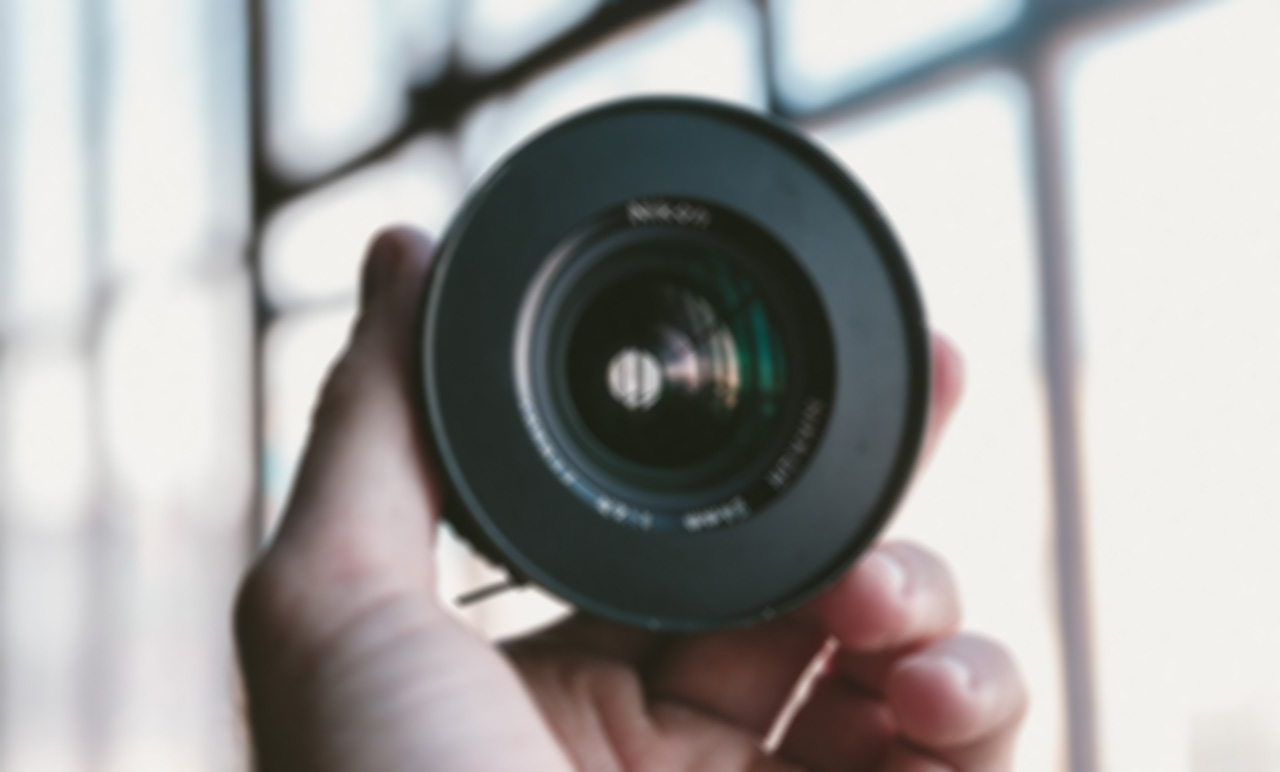
**Material and Durability**
Plastic Lenses
Plastic lenses are predominantly fabricated from high-performance engineering plastics such as ABS (acrylonitrile butadiene styrene copolymer) or PC (polycarbonate). These materials are extensively utilized in consumer electronics due to their favorable physical characteristics and economic viability. Specifically, ABS exhibits superior impact resistance and ease of processing, whereas PC is renowned for its exceptional transparency and heat resistance. Despite these advantages, plastic lenses generally exhibit lower durability compared to metal alternatives. For example, during routine use, the surface of plastic lenses is more susceptible to scratches, particularly when exposed to hard objects without protective measures. Furthermore, prolonged exposure to high temperatures or ultraviolet radiation may cause aging or deformation, potentially compromising the overall performance of the lens.
Metal Lenses
In contrast, metal lenses are typically constructed from high-strength alloys such as aluminum or magnesium. These materials possess excellent mechanical properties, including high strength, wear resistance, and impact resistance, which enhance their resilience against wear and drops during daily use. Aluminum alloy, for instance, has become a preferred choice for many high-end devices due to its optimal balance of density and processability. Magnesium alloys, on the other hand, are celebrated for their lightweight and robustness, making them ideal for applications requiring both reduced weight and enhanced structural integrity. However, the higher density of metal materials results in increased overall weight, and the complex manufacturing processes significantly elevate production costs compared to plastic lenses.
**Weight and Cost**
Plastic Lenses
Owing to the utilization of lightweight materials, plastic lenses excel in weight management. This characteristic is particularly advantageous for portable devices, as a lighter weight enhances user experience and alleviates fatigue associated with prolonged usage. Additionally, the relatively low production cost of plastic lenses contributes to more competitive pricing, making them especially suitable for budget-conscious consumers. Many entry-level cameras and smartphones, for example, incorporate plastic lenses to minimize manufacturing expenses while maintaining a price advantage.
Metal Lenses
Metal lenses, conversely, exhibit substantially greater weight due to the use of high-density materials. While this feature may introduce inconvenience for some users, it proves critical in professional settings. In photographic equipment and industrial devices, metal lenses offer enhanced stability and reliable performance under demanding conditions. Nevertheless, the elevated cost of metal lenses remains a significant consideration. From raw material procurement to precision machining, each step demands substantial resources, ultimately resulting in higher product prices. Consequently, metal lenses are predominantly found in mid-to-high-end markets, catering to users prioritizing quality and performance.
**Thermal Performance**
Plastic Lenses
A notable limitation of plastic lenses is their inferior thermal conductivity. In high-temperature environments, plastic materials struggle to dissipate heat effectively, leading to potential heat accumulation that may compromise the stability and lifespan of the equipment. For example, prolonged video recording or intensive computational tasks may degrade the performance of internal electronic components or even cause damage due to overheating. To mitigate this issue, manufacturers often integrate additional heat dissipation structures into the design of plastic lenses, though this increases complexity and cost.
Metal Lenses
Metal lenses demonstrate superior thermal performance due to the inherent high thermal conductivity of metallic materials. For instance, aluminum alloy exhibits a thermal conductivity of approximately 200 W/(m·K), far exceeding that of most plastic materials (typically less than 0.5 W/(m·K)). This efficient heat dissipation capability renders metal lenses highly suitable for high-performance applications, such as professional cameras, surveillance systems, and medical imaging equipment. Even under extreme conditions, metal lenses maintain stable operation, thereby extending the service life of the equipment.
**Summary**
In conclusion, plastic and metal lenses each possess distinct advantages and limitations. Plastic lenses, characterized by their lightweight and cost-effectiveness, are well-suited for consumer electronics and portable devices. Metal lenses, distinguished by their exceptional durability and thermal performance, serve as the preferred option for professional domains and premium markets. Users can select the most appropriate lens type based on specific application requirements and budget constraints to achieve optimal performance.
Post time: Apr-21-2025